15 Reasons HeadLOK Construction Screws are a DIY Game Changer
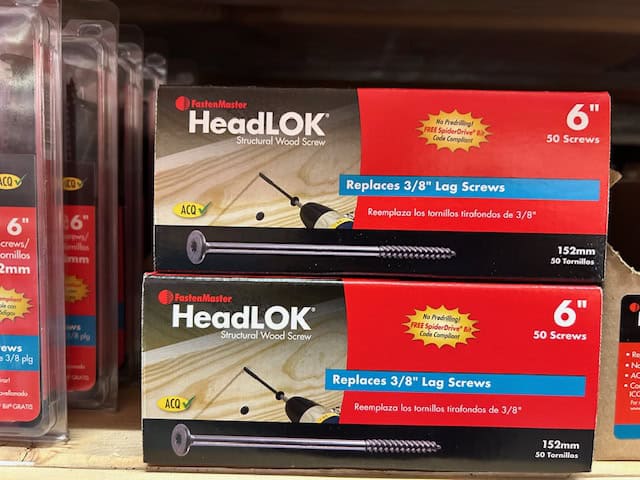
This blog is about hardware that I didn’t even know existed ten years ago. Now I rarely complete a building project of any size without them. HeadLOK structural screws have been a game changer when it comes to quickly building things that are reliable and strong. Here are 15 reasons that HeadLOK can bring your construction game up a notch. 1. Sheer strength HeadLOKs replace 3/8-inch construction screws. Sheer strength refers to its ability to withstand force. Think, ‘How much would it take to snap this thing or to make the head come off’. Considering that a quality 3/8-inch bolt can withstand up to 7000 pounds of pressure (and the average car is around 4000 pounds), HeadLOK’s more than do the trick. 2. Code compliant HeadLOK were first introduced in 2007 and have quickly become a building crowd favorite. They were the first flat headed fastener to meet code. They are compliant most of the time– meeting International Building Code (IBC) and the International Residential Code (IRC). You will still want to double-check your local building codes though. 3. Thin profile HeadLOK shank diameter (the thickness where the threads are) is far less than its 3/8-inch lag screw equal. HeadLOK diameter is 0.190 inches verses the 3/8-inch lag screws coming in at .3750 inches. This reduces splitting and makes predrilling unnecessary. 4. Wide head A HeadLOK has a wide, thin head (kind of like my friend, Darin). It’s 5/8- inch wide and about 3/16- inch thick. (a 3/8-inch lag head is just under ½-inch – .469 inches). Because it has more surface and is incredibly strong, the HeadLOK head has more pulling power. Its flat profile and aggressive downward pull (thanks to deeper threads) leads to a flush surface. No countersinking needed most of the time. 5. No pre drilling needed This is a result of a thinner shank as well as a supped-up design. HeadLOKs have a sharp gimlet point (that bores and digs in quickly) and deep-thread design (that pulls and holds with a lot more power) making building fast and effective with no prep needed. Authors note: I saw ‘gimlet point’ on the box and had no idea what it meant. As an adjective it means having a piercing or penetrating quality. As a noun, gimlet is a drink consisting of sweetened lime juice and gin or vodka, and sometimes carbonated or plain water. They probably mean the adjective. 6. Quick building With the bit that’s provided and an 18V drill or higher, you’re ready to build. Point and squeeze. In some applications, HeadLOKs can take the place of joist hangers (see below). This saves a ton of time and pulls everything tightly together. 7. Aggressive pull The deep thread and quality metal makes HeadLOK a giant in the pulling and holding department. In the project below, 10” HeadLOKs were used to fasten a beam (3 glued and screwed PT 2x 6) to posts, used for a foundation for the Water Shed. These were countersunk to avoid any slight unevenness when it was time to lay the floor joists. 8. SpiderDrive HeadLOKs uses an internal drive (they call it SpiderDrive). A special bit fits into the drive, making 8 points of contact. This makes things fast, easy and reliable. 9. 8 point driver This fits into the SpiderDrive. The driver is included in boxes of 50 screws or can bought separately (2 for about $8.50). 10. Reusable At a big box store this week, a single 8” HeadLOK was $2.72. A box of 50 was $50.57 – or $1.02 for one. Fortunately, it’s very easy to back HeadLOKs out and use them again in order to save a few bucks. The Spider drive may grind down after many uses but it takes awhile for this to happen. (I’ll use them to fasten temporary brackets when putting on a metal roof). I know I’ll use them eventually, so I usually go with boxes of 50. 11. Pulls things square Because of their pulling power, HeadLOK pulls framework together and holds it there. With good straight cuts, this can go a long way toward squaring things up, squeezing out small spaces to make things more uniform. 12. A quick and easy way to level a deck There are no level spaces on our property and rocky ground makes it almost impossible to level by hand. HeadLOK give a quick and easy way to put up the deck for smaller buildings not needing foundations. Place concrete deck blocks. Build a frame the dimensions of the building using HeadLOKs. Put 4 x 4s in the deck blocks. Raise the frame until level. HeadLOK the frame to the posts. Add the rest of the floor joists with (drumroll) HeadLOKs! 13. Multiple lengths to choose from HeadLOKs are readily available in 2 7/8” up to 10”. 4 ½ “ work well for attaching to a 4 x 4 post. For fastening at the perpendicular (see photo above) 6” are perfect. You will want to be certain that they are long enough to hold but aren’t long enough to punch through the other side. 14. Corrosion resistant HeadLOKs are designed to resist rust and corrosion for the life of a project (which, if all goes well, will be a very long time). They’re made from carbon steel with a coating that increases corrosion resistance. They are ACQ approved – which means they’re designed to be used with treated wood without premature corrosion. 15. Multiple Uses I’ve used HeadLOKs for a variety of projects. To hold foundations together. To fasten bunks to a wall. To attach walls when framing. When building decks, etc. The common theme is needing structural strength that can be relied upon. Ten years ago we were strangers. Now HeadLOKs are my good friends and live with me in their own plastic box. Happy Building I hope you find HeadLOK construction screws as useful as I have. It’s always great to hear from
Beginner’s Guide to Amish Rough-Cut Lumber
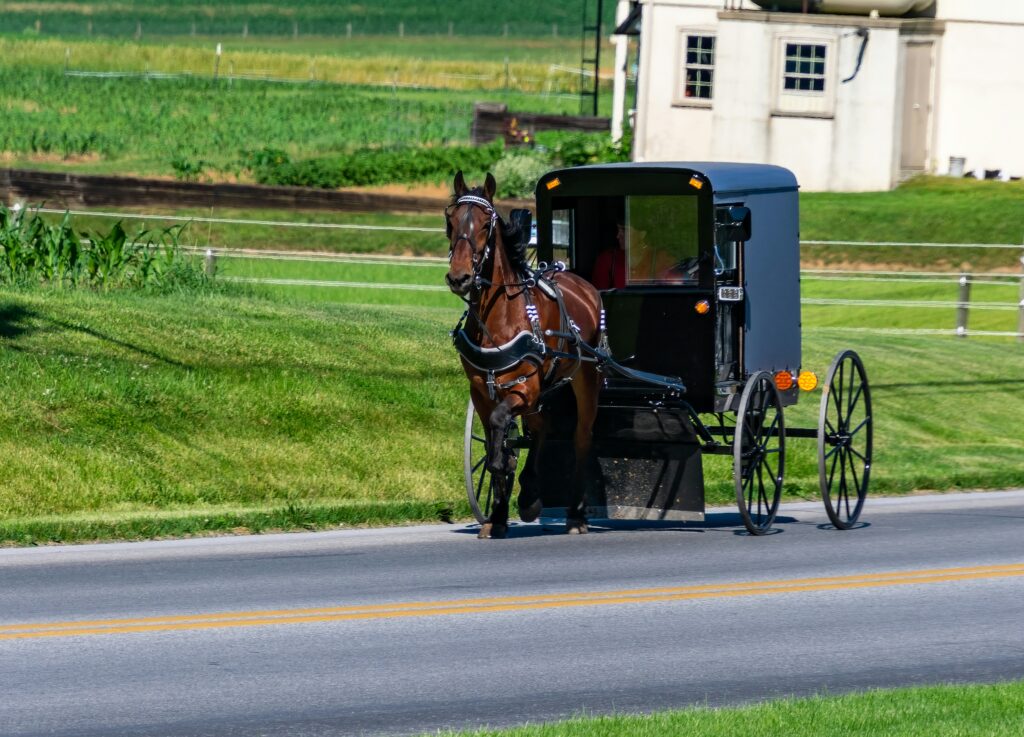
Amish Rough-Cut Lumber This post is all about Amish rough-cut lumber – what makes it different from big box lumber, how to find it, what to know when ordering, and some things to know when doing business with the Amish. Because of its rustic appearance and much more reasonable price tag, rough cut lumber has been the perfect choice for quite a few projects around the camping cabin cluster. Amish sawmills are definitely not the only option when purchasing rough- cut – there are other amazing lumber mills out there – but for this post we’ll be focusing on our experiences with the Amish. Information in this post can help you decide if Amish rough- cut lumber is the right choice for your project and how to get it if it is. What is rough cut lumber and how is it different from lumber from a big box store? Picture going into the woods, cutting down a live tree, and running it through a gas powered saw mill. One pass. No drying. No planing. It’s rough surface, with some pulliing and blade marks, can make it a rustic, very cool looking material choice. The boards you get from the big box stores are kiln dried, rated for strength and quality, planed, smooth finish and about three times the price. This can be a good choice when considering the ready-to-use ease, convenience, and finer finish. Personally, I love the way a rough-cut board and batten building looks, like it could have been built 200 years ago, but it isn’t my go-to for every project. Theres more to know when deciding if Amish rough-cut lumber is the best choice for what you’re working on. Amish rough-cut lumber price Price is a BIG plus when using rough-cut. This can vary from region to region and mill to mill, but rule of thumb for us has been Amish rough-cut being about one third of the price compared to what we would have spent in a big box lumber yard. Appearance Rough cut looks how it sounds. Pretty rough. Cut with a coarser saw and not planed, the surface is rough to the touch. The grain of the wood shows through well, but definitely not ideal for a fine finish look. It’s dimensions can also be a perk, especially for 2 by (two inches thick – more on that below). This can give a project a non-standard and unique feel (the bunks pictured below were made from rough-cut and took A LOT of sanding). For some projects I’ve combined pressure treated, KD lumber, and rough cut. This is to get a rustic effect, keep the price down somewhat, and to build a structure that will last a very long time. An example of this is the firewood shelter built in close proximity to the firepit (in the photo above). It’s not stained yet but gives us a perfect place to always have dry firewood ready! Dimensions Rough cut measurements are true. Meaning a 1 inch board is actually one inch thick, a 2 inch board is actually 2 inches thick, etc. A 1- inch board bought at a big box is actually ¾ inch thick. A 2- inch board is 1 and a half inches thick. The same goes for width. An 8 inch rough cut board is really 8 inches wide. An 8 inch board at a big box is 7 and a half inches wide. This is basic information for folks with wood buying experience but maybe not common knowledge across the board (see what I did there? 😊 ) 8 feet long means 8 feet long in both worlds, although you will see more variance with rough cut. Big box boards run just a little long (by an inch or so) giving a little leeway to square off ends if needed. Something else to keep in mind is that the dimensions of rough cut are close but not exact. You will want to measure to see if thickness and width are uniform. This can vary from one end of the board to the other by a considerable amount so it’s a good idea to double check. Moisture Content (and challenges it could cause) This is a big one. Rough cut lumber is cut from logs that have recently been living and growing. When boards and dimensional lumber are cut, the moisture content is usually extremely high. What does this mean? Rough cut lumber is A LOT heavier than kiln dried lumber. It also tends to warp and to crack more as it dries. If stacking before using, it’s a great idea to put spacing sticks between boards. This encourages air flow – which allows for drying and also cuts down on mold growth. Off the ground, stacked with spacers, and protected from rain and scorching sun is your best bet. We learned this one the hard way, when green and black mold began to grow in less than a week between boards we had stacked without spacing. The Amish are known to build with wet wood, with the trick being to assemble and secure with nails and joinery before wood has a chance to warp. Our two camping cabins were framed this way – a few boards cracked over time but nothing that couldn’t be fixed with a few extra nails and a tube of caulk. Not Graded A lot of rough cut lumber is up to the challenge of being build- worthy, but not all. Some lumber will be frail and will crack, depending on the tree and the portion of the log it was cut from. Buyer beware on this. Big box isn’t infallible but is graded, which indicates it’s suitable for building. Not Insect Resistant It’s amazing what a carpenter ant or a carpenter bee can do to a piece of rough cut. Especially prior to being stained or painted, rough cut can be a delicious snack for insects. Not thinking things